Контроль качества в машиностроении — это не просто процедура, а целостная система, влияющая на все аспекты производства. От стандартов до постоянного улучшения каждого этапа — от этого зависит не только качество конечного продукта, но и конкурентоспособность компании на рынке.
Краткий обзор ключевых компонентов, включая стандарты, процессы, коммуникации и постоянное улучшение, поможет глубже понять, как они взаимодействуют и чем могут быть полезны. Узнаете о том, как правильно внедрять и развивать эти аспекты управления качеством, чтобы добиться оптимальных результатов.
Особое внимание уделим практическим советам, которые могут быть полезны на каждом этапе производственного цикла. Благодаря этой информации можно будет не только улучшить качество продукции, но и повысить эффективность всего процесса производства.
- Стандарты качества в машиностроении
- Процессный подход в контроле качества
- Коммуникация на всех уровнях
- Постоянное улучшение и его роль
- Практические советы и примеры
Стандарты качества в машиностроении
В сфере машиностроения стандарты качества играют ключевую роль в обеспечении надежности и безопасности продукции. Каждый элемент конструкции должен соответствовать строго установленным нормам и правилам, что требует тщательной проверки и регулярного мониторинга. В основе этих стандартов лежат международные документы, такие как ISO 9001, которые регламентируют не только производственные процессы, но и все аспекты управления качеством.
ISO 9001 широко признан в мире как один из самых авторитетных стандартов в области контроля качества. Эти стандарты помогают предприятиям оптимизировать процессы и создавать продукцию, соответствующую потребительским ожиданиям. Использование ISO 9001 позволяет компаниям минимизировать риски брака и повышает репутацию бренда. Одним из важнейших аспектов внедрения стандартов является их адаптация под уникальные условия каждой компании, что требует комплексного подхода и участия всех сотрудников.
Внедрение стандартов качества в машиностроении способствует не только повышению производительности, но и снижению издержек на всех этапах технологического цикла. Секрет кроется в том, чтобы вовремя выявлять и устранять недочеты в системах контроля. Это требует интеграции инновационных технологий, таких как автоматизация и цифровизация, которые позволяют делать процессы более прозрачными и управляемыми. Как отметил известный специалист по качеству доктор Деминг:
"Качество нечто большее, чем только продукт; это обязательство перед клиентом".Это заявление демонстрирует важность переноса усилий на каждую деталь, которая напрямую влияет на финальный результат.
При внедрении стандартов качеству присваивают разнообразные индексы и метрики, которые служат основой для последующего анализа и улучшения. Это могут быть параметры, касающиеся прочности, долговечности, функциональности изделий и их узлов. Все данные о тестах и испытаниях должны систематически фиксироваться и анализироваться для формирования выводов о состоянии процессов. Комплексный подход к контролю таких параметров позволяет для каждой детали создавать профиль качества, что существенно упрощает дальнейшую работу.
Значимость стандартов очевидна, однако их поддержание требует инвестиции не только материальных ресурсов, но и дисциплины со стороны заказывающей и производящей стороны. Ответственность за соответствие стандартам несет команда сотрудников, начиная от инженеров и заканчивая контролерами качества. Управление качеством — это цепочка взаимодействующих звеньев, которая держится на внутренней мотивации и готовности не стоять на месте. Только при активном включении всего персонала машиностроительная компания способна оставаться конкурентоспособной и динамично развиваться в условиях постоянно меняющегося рынка.
Процессный подход в контроле качества
Основой процессного подхода в контроле качества является управление всеми аспектами производственного цикла как множеством взаимосвязанных процессов. Каждое производство — это система, где каждый этап является частью более сложного механизма. У каждого этапа свои ресурсы, процессы и результаты, которые оказывают влияние на следующий этап. Это способствует более глубокому пониманию всей производственной процессы в целом и позволяет выделить ключевые элементы, требующие особого внимания. Подход определяет, какие аспекты нуждаются в оптимизации для повышения эффективности: начиная от управления ресурсами до способности компании быстро адаптироваться к изменениям в требованиях клиентов и рынка.
В процессе внедрения процессного подхода важной задачей является создание информационной системы управления, поддерживающей все бизнес-процессы. Это позволяет подробно отслеживать каждый этап и его вклад в конечный результат. Подобные системы дают возможность не только получать оперативные данные о состоянии производства, но и прогнозировать его работу. Организация, использующая процессный подход, способна быстрее адаптироваться к изменяющимся условиям, что в свою очередь, повышает ее конкурентоспособность.
Примером успешного применения процессного подхода в управлении качеством может служить опыт, накопленный в автомобильной промышленности. Использование этого метода позволило улучшить координацию внутрикорпоративных процессов, сделав их более прозрачными и управляемыми. Интересен тот факт, что по данным исследования McKinsey, компании, внедряющие процессный подход, сокращают затраты на 30% и увеличивают производительность труда на 25%.
На практике внедрение процессного подхода требует внимания к таким факторам, как установление четких границ ответственности, привлечение сотрудников к участию в улучшении процессов и мотивационная система, ориентированная на долгосрочный результат. Качество всей системы зависит от грамотного распределения ролей и эффективного разделения обязанностей, что обеспечивает высокий уровень дисциплины внутри коллектива. По словам специалиста в области машиностроения, Джона Спина:
"Настоящий контроль качества начинается с четкого понимания процессов, и только когда мы можем визуализировать весь цикл, мы становимся способными управлять им".
В этом контексте важно помнить, что каждый процесс — это живой механизм, который требует постоянного улучшения. Компании следует активно экспериментировать с новыми методами и инструментами, интегрируя их в свои производственные процессы. Такой подход не только улучшает качество продукции, но и стимулирует инновации, что в конечном итоге приводит к более устойчивому развитию организаций, действующих в сложных рыночных условиях.
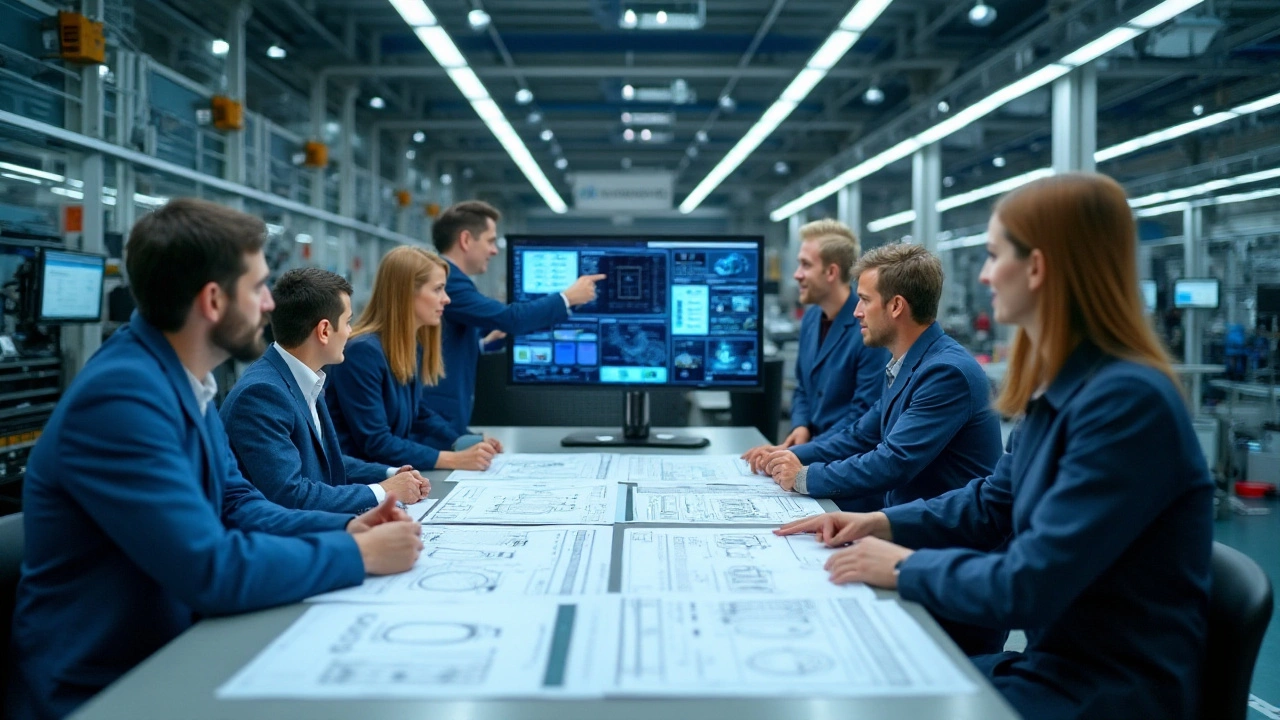
Коммуникация на всех уровнях
Эффективная коммуникация является основой успешного управления качеством в любой промышленной отрасли, и машиностроение не является исключением. В компании, где связность и обмен информацией поставлены на высоком уровне, легче добиваются стабильного качества продукции и минимизации ошибок на всех стадиях производства. Это связано с тем, что все заинтересованные стороны — от инженеров до операторов — имеют чёткое представление о своих задачах и конечных целях. Но качество коммуникации определяется не только внутренними факторами, но и междунарожной конкуренцией, что требует нового подхода и инновационных методиков в канализации информационного обмена.
Исследования показывают, что компании с отлаженной системой коммуникации меньше подвержены рискам, связанным с производственными сбоями и несоответствиями в контроле качества. К примеру, согласно отчёту Ассоциации менеджеров качества, улучшение уровня общения между отделами сокращает производственные ошибки на 25%.
"Правильная коммуникация не только раскрывает потенциал компании, но и служит основой для создании динамичной и более ответственной команды," — утверждает профессор Прайс из Гарвардской бизнес-школы.Интеграция современных технологий, таких как системы управления проектами и специальные приложения для обмена информацией, может значительно повысить уровень осведомленности сотрудников и ускорить процесс решения проблем. На этапе внедрения новых стандартов и инструкций, коммуникация между различными уровнями компании способствует не только быстрому освоению новшеств, но и позволяет более эффективно использовать имеющиеся ресурсы.
Однако важно помнить, что хороший уровень общения не зависит только от технологий. Важную роль играют и тактика взаимодействия, и организационная культура. Компаниям стоит учитывать такие аспекты, как регулярное проведение совместных совещаний и сессий обратной связи. Эти меры способствуют укреплению рабочей атмосферы и создают у сотрудников ощущение вовлеченности в достижение общих целей. При наличии прочной системы обратной связи, руководство может более оперативно реагировать на текущие проблемы и корректировать свой подход к контролю качества.
Аспект | Преимущество |
---|---|
Ежедневные встречи | Повышение вовлеченности сотрудников на 15% |
Использование цифровых платформ | Сокращение времени на внутреннее общение на 30% |
Постоянное улучшение и его роль
В сфере управления качеством в машиностроении, концепция постоянного улучшения играет критическую роль. Это динамичный процесс, который стимулирует компании к постоянному анализу и оптимизации всех аспектов производства. В этой связи, одним из наиболее известных подходов является методология Kaizen — японское слово, означающее 'улучшение'. Оно охватывает идеи непрерывных изменений и вовлечения каждого сотрудника в процесс совершенствования продуктивности и качества.
Рассмотрим, как постоянное улучшение применяется на практике. Например, эффективные команды по контролю качества проводят регулярные встречи для обсуждения достигнутых результатов и выявления потенциальных проблем. Они стремятся не только исправить недостатки, но и предотвратить их возникновение. Данный проактивный подход требует активного участия всех членов команды и руководства. Это создаёт здоровую рабочую среду, где инициативы, направленные на улучшение, ценятся и поощряются.
"Современные предприятия должны быть гибкими и находчивыми. Это требует культуры постоянного обучения и улучшения возможностей," — говорит Питер Друкер, известный специалист в области менеджмента.
Переходя к конкретным практическим инструментам, важно упомянуть систему PDCA (Plan-Do-Check-Act), которая часто используется в машиностроении для структурирования постоянного улучшения. На стадии планирования компании устанавливают измеримые цели и стратегии для их достижения. Затем следуют выполнение, проверка результатов и корректировка процессов по мере необходимости. Такой цикличный подход гарантирует, что ничего не остаётся без внимания и все возможные проблемы оперативно решаются.
Также распространённым инструментом является внедрение анализа «пяти почему», который помогает глубже понять коренные причины проблем. Этот метод выделяет область, где необходимо сконцентрировать усилия, и способствует систематической коррекции. Регулярное внедрение этих и других методов значительно усиливает позиции компании на конкурентном рынке и улучшает качество производимой продукции.
Без постоянного улучшения ни одна компания не сможет оставаться успешной в долгосрочной перспективе. Это не дань моде, а необходимость, предполагающая гибкость и адаптацию в условиях постоянно меняющихся технологий и требований рынка. Согласно исследованиям, компании, внедрившие культуру постоянного улучшения, показывают рост эффективности на 20-30% в первые годы внедрения таких программ. Это существенное преимущество в жесткой конкурентной борьбе.
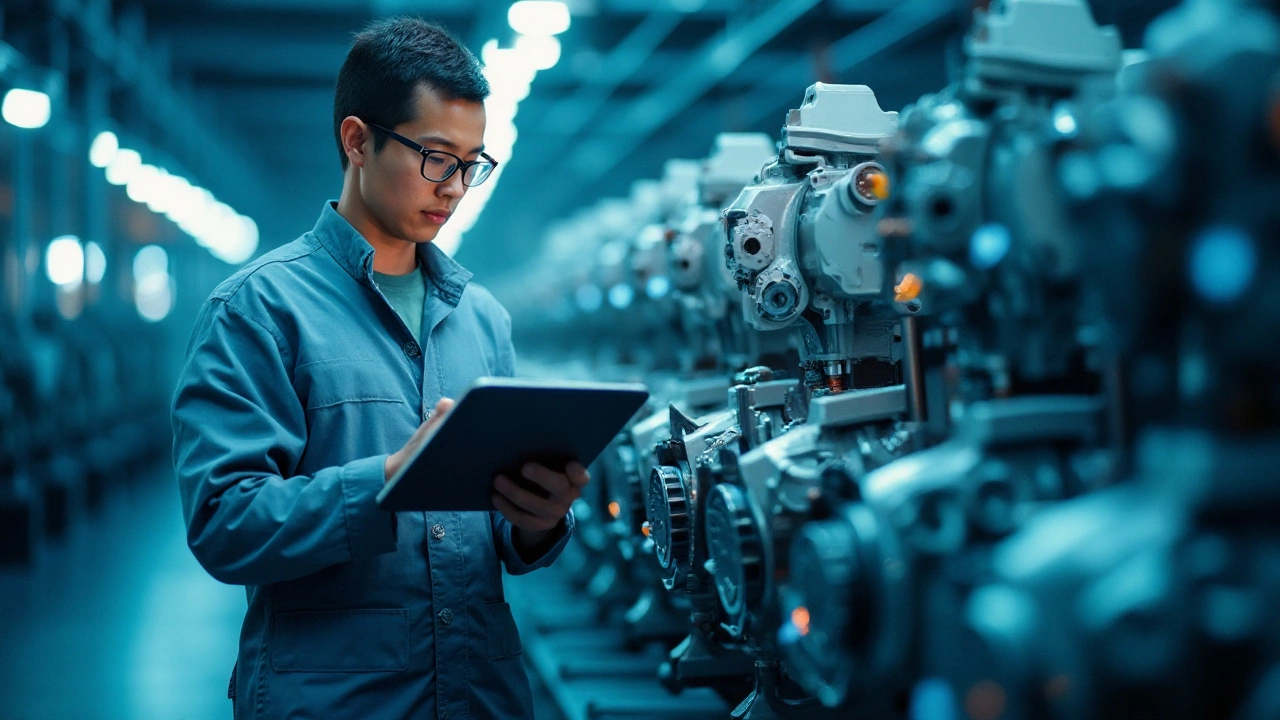
Практические советы и примеры
Введение системы контроля качества в производственные процессы отличается от компании к компании, но основные принципы остаются неизменными. Один из важнейших элементов — это создание стандартов, которые будут использоваться на каждом этапе производства. Для этого необходимо определить критические точки контроля, где продукция наиболее уязвима для дефектов. При этом следует учитывать не только технические аспекты, но и человеческий фактор, который часто является ключевым в предотвращении ошибок. Системный подход позволяет компании быстро реагировать на выявленные отклонения и адаптировать свои процессы в соответствии с выявленными проблемами.
Помимо определения стандартов, важна эффективная коммуникация между отделами. Этот аспект часто становится упущением во многих компаниях, однако именно четкая передача информации позволяет быстро реагировать на изменения и усовершенствования. Для этого можно использовать различные инструменты, такие как регулярные встречи, внутренние записи или электронные системы оповещения, которые своевременно доносят информацию до всех вовлеченных сторон. Также стоит отметить, что наличие обратной связи от сотрудников, работающих на производственной линии, может стать ценным источником информации для управления качеством.
Примеры успешного внедрения
Рассматривая успешные примеры внедрения системы управления качеством, стоит упомянуть японскую концепцию «кайдзен», которая переводится как «непрерывное улучшение». Эта практическая философия сосредоточена на постоянном улучшении всех аспектов производственного процесса, включая оборудование, технологии и обучение сотрудников. Статистика показывает, что компании, принявшие такой подход, подняли качество своей продукции на 30% в течение первого года.
«Секрет успеха в бизнесе заключается в детальном анализе процессов и постоянном стремлении к их совершенствованию». — Таити Оно, основатель концепции «кайдзен»
На практике внедрение «кайдзен» может осуществляться через небольшие этапы, каждый из которых тщательно анализируется, что делает процесс управляемым и гибким. В компаниях, реализовавших эту концепцию, внедрение инноваций осуществляется не только на уровне старшего менеджмента, но и задействует работников всех уровней.
Год | Увеличение качества |
---|---|
2020 | 10% |
2021 | 15% |
2022 | 30% |
Еще один важный совет — внедрение технологий. С развитием технологий контроль качества стал значительно проще и эффективнее. Многие современные предприятия используют автоматизированные системы, которые позволяют отслеживать качество в реальном времени, отправлять уведомления о возможных проблемах и даже автоматически корректировать параметры производства для минимизации ошибок. Это позволяет не только снизить вероятность человеческой ошибки, но и увеличивать объем выпуска продукта без снижения его качества.