В машиностроении 3D моделирование — это уже не просто модная фишка, а стандарт работы. Заводы на каждом шагу используют цифровые модели: от идеи нового механизма до сервисного обслуживания готовой техники. 3D-модели просто экономят нервы и деньги. Обнаружить ошибку на компьютере — в сто раз дешевле, чем переделывать уже готовую железку.
Вся соль в том, что с помощью 3D можно посчитать не только, как деталь будет выглядеть, но и как она поведёт себя под нагрузкой. Такие модели легко поделиться с коллегами, заказчиками или подрядчиками, не таскаясь с чертежами из толстой папки. Всё — в цифре, и всё можно быстро поменять. Это не просто удобно, а реально ускоряет разработку новых машин.
- Цифровой двойник: зачем он заводу
- 3D моделирование на этапе проектирования
- Прототипирование и тестирование деталей
- Автоматизация и подготовка к производству
- Интеграция в сервисное обслуживание
Цифровой двойник: зачем он заводу
Когда на заводе говорят про 3D моделирование, почти всегда всплывает понятие цифрового двойника. Это не просто 3D-портрет детали, а полная цифровая копия всего агрегата или даже целого станка со всеми его внутренностями и особенностями работы.
Цифровой двойник помогает делать такие штуки, которые раньше казались фантастикой. Например, можно в реальном времени следить, как «чувствует себя» производство — если где-то деталь перегревается или мотор ведёт себя странно, двойник быстро это покажет. Такой подход сильно сокращает время реакции на сбои и поломки.
Вот на что реально способен цифровой двойник:
- Показывает, как оборудование будет работать без единого реального запуска;
- Помогает спрогнозировать поломки заранее, просчитывает износ и стрессы в деталях;
- Позволяет быстро вносить изменения в конструкцию и тут же видеть результат;
- Согласовывает работу целой команды — все видят одну и ту же модель, не путаются в версиях;
- Экономит средства: меньше тестовых образцов, меньше брака на производстве.
Реальные заводы уже используют цифровые двойники. Например, на европейских машиностроительных предприятиях применение 3D двойников сократило простои на 25%. Это ощутимая экономия для любого бизнеса.
Преимущество | Практический эффект |
---|---|
Оперативный анализ работы | Быстро замечают сбои, быстрее чинят |
Предиктивное обслуживание | Меньше неожиданных поломок |
Оптимизация производства | Точно рассчитывают, что и когда делать |
Цифровой двойник — мощный инструмент для современных заводов. Без него конкурировать на рынке уже становится тяжело, потому что время на запуск новых технологий уменьшается в разы. И да, всё это стало возможно благодаря 3D моделированию, которое уже давно стало рабочим инструментом, а не узкой сферой для инженеров-энтузиастов.
3D моделирование на этапе проектирования
Этап проектирования — это всегда тест на внимательность: тут важно не упустить мелочи, которые потом могут вылезти головной болью. Вот тут 3D моделирование экономит кучу времени. Вместо тысячи плоских чертежей инженеры делают одну цифровую модель детали или узла. Можно двигать, крутить и сразу смотреть, как всё стыкуется между собой.
Главное, что такие модели позволяют буквально «примерить» новую запчасть к остальной конструкции, даже если саму железку еще никто не подержал в руках. Например, крупные машиностроительные заводы вроде «КАМАЗ» давно используют 3D, чтобы создавать сборочные единицы заранее, прогнозировать, где возникнут зазоры или пересечения.
Типичный процесс выглядит так:
- Создают 3D-модель детали в специальной программе (чаще всего это SolidWorks или Siemens NX).
- Проводят анализ прочности и кинематики прямо в цифровом виде — это называется CAE-расчет (компьютерный инжиниринг).
- Пробуют собрать всю конструкцию виртуально, чтобы убедиться, что ничего не будет мешать друг другу.
- Согласовывают модель с разными отделами через общий цифровой проект — и тут работает принцип «смогли посмотреть все».
Факт, который приятно знать: с помощью 3D моделирования время на проектирование сложной детали сокращается минимум в 2-3 раза по сравнению со старым методом вручную, а человеческий фактор почти не влияет.
Раньше (2D) | Сейчас (3D) |
---|---|
3-4 недели на согласование и внесение правок | 1 неделя или меньше |
Ошибки при сборке часто были сюрпризом | Все пересечения видны заранее |
В итоге современное 3D моделирование на проектном этапе не только ускоряет процесс, но и делает его намного прозрачнее для всех участников. Все изменения быстро согласуются, а заказчик или производственный отдел видят итог «вживую», пусть и на экране.
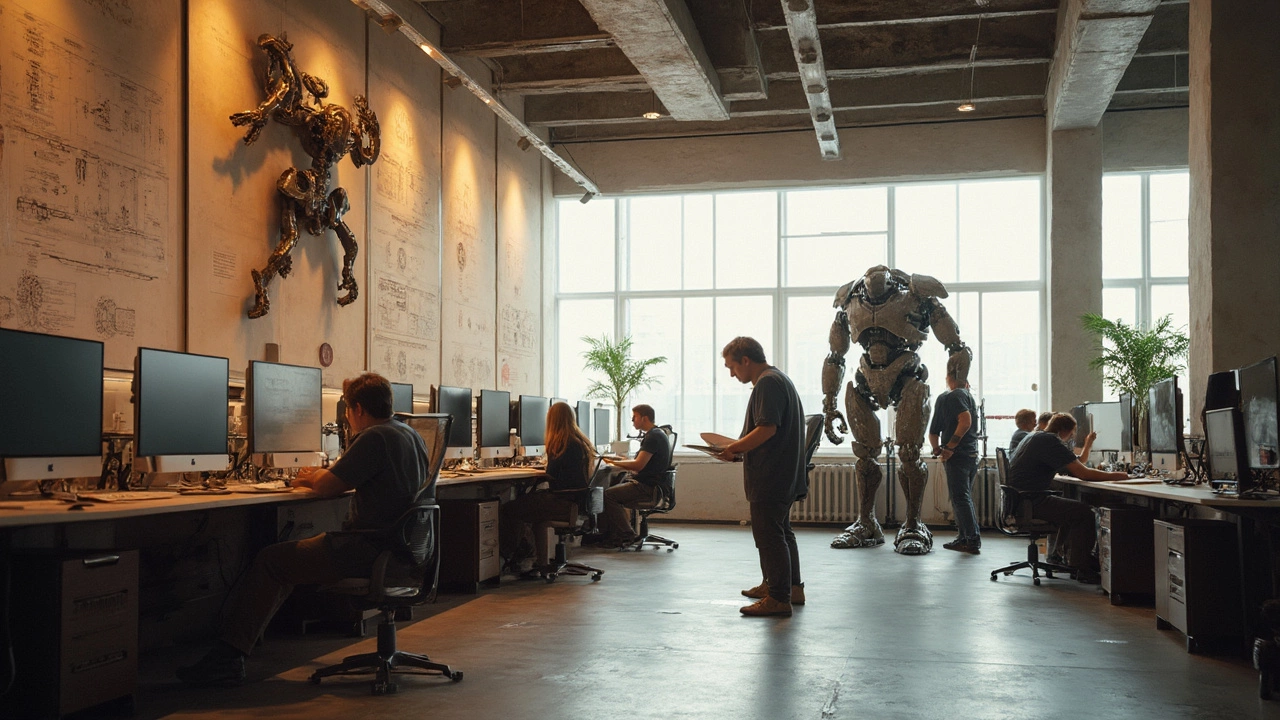
Прототипирование и тестирование деталей
Когда речь заходит о 3D моделировании в машиностроении, первая польза — быстрое и недорогое создание прототипов. Банально, но теперь не нужно неделями ждать деталь с завода: напечатал на 3D-принтере, и уже можно крутить в руках, примерять к сборке. Даже крупные автогиганты вроде BMW и Ford используют 3D модели для тест-драйва новых узлов ещё до производства по-настоящему.
Вот как обычно выглядит процесс прототипирования с помощью 3D:
- Конструктор строит цифровую модель детали.
- Модель отправляется на 3D печать или фрезеровку.
- Готовый прототип тестируют на прочность, точность и удобство сборки.
- Ошибки быстро исправляют в файле и запускают новую версию, без лишних затрат времени.
Тестируют практически всё: от прочности и усталости до реакций в экстремальных режимах. С помощью 3D моделирования делают даже виртуальные "краш-тесты" сложных сборок или механизмов.
Согласно реальным данным, переход к 3D-технологиям позволяет сократить время на разработку прототипа в 3-4 раза, а стоимость отдельных моделей — почти в 2 раза. Посмотрите сами:
Параметр | Традиционные методы | 3D моделирование |
---|---|---|
Время на изготовление | 3-4 недели | 5-7 дней |
Средняя стоимость прототипа | 100 000 руб. | 50 000 руб. |
Здесь важный момент: эти прототипы можно не просто трогать. Их можно "ломать" на виртуальных стендах, чтобы заранее найти слабые места. Некоторые компании даже гоняют цифровые копии деталей на износ в тестовых условиях, чтобы не списывать целые партии по факту.
Автоматизация и подготовка к производству
Когда завод доходит до запуска детали в серию, без 3D моделирования уже никак. Это не просто картинка для инженеров — вся система производства строится вокруг цифровой модели. Благодаря этому предприятие тратит меньше времени на наладку и почти не ошибается в позиционировании оборудования.
Производственный цех можно спроектировать виртуально: заранее расставить станки в 3D, проверить, хватает ли места для техники, как пойдет логистика. Потом можно в один клик выгрузить модель и передать технологам или программистам станков с ЧПУ. Система сама подготовит управляющие файлы для резки, гибки, фрезеровки и сварки.
3D моделирование экономит и на подготовке документации. Если на заводе есть PLM-система, вся структура изделия — детали, сборки, спецификации — в реальном времени обновляется вместе с моделью. Меньше бумажек, меньше ошибок.
- Время подготовки производства сокращается минимум на 30% при переходе на цифровые методы.
- Автоматизируются процессы закупки: система видит все детали в модели и сразу формирует заявки поставщикам.
- Согласование с подрядчиками или службами проходит быстрее — все видят одну и ту же актуальную 3D-модель.
Есть интересная статистика: завод, который внедрил полную автоматизацию на базе 3D моделирования, может уменьшить количество брака на 20–40%. Причина простая — нет разночтений между инженерией и производством, все работают с одной версией изделия.
Показатель | До внедрения 3D | После внедрения 3D |
---|---|---|
Время на наладку линии | 10 дней | 5-6 дней |
Кол-во ошибок в техпроцессе | 10+ | 2-3 |
Процент брака | 8% | 4,5% |
В итоге, 3D моделирование реально помогает наладить четкую, быструю и понятную работу в современном машиностроении. Буквально спасает от лишних затрат, потери времени и головной боли инженеров.
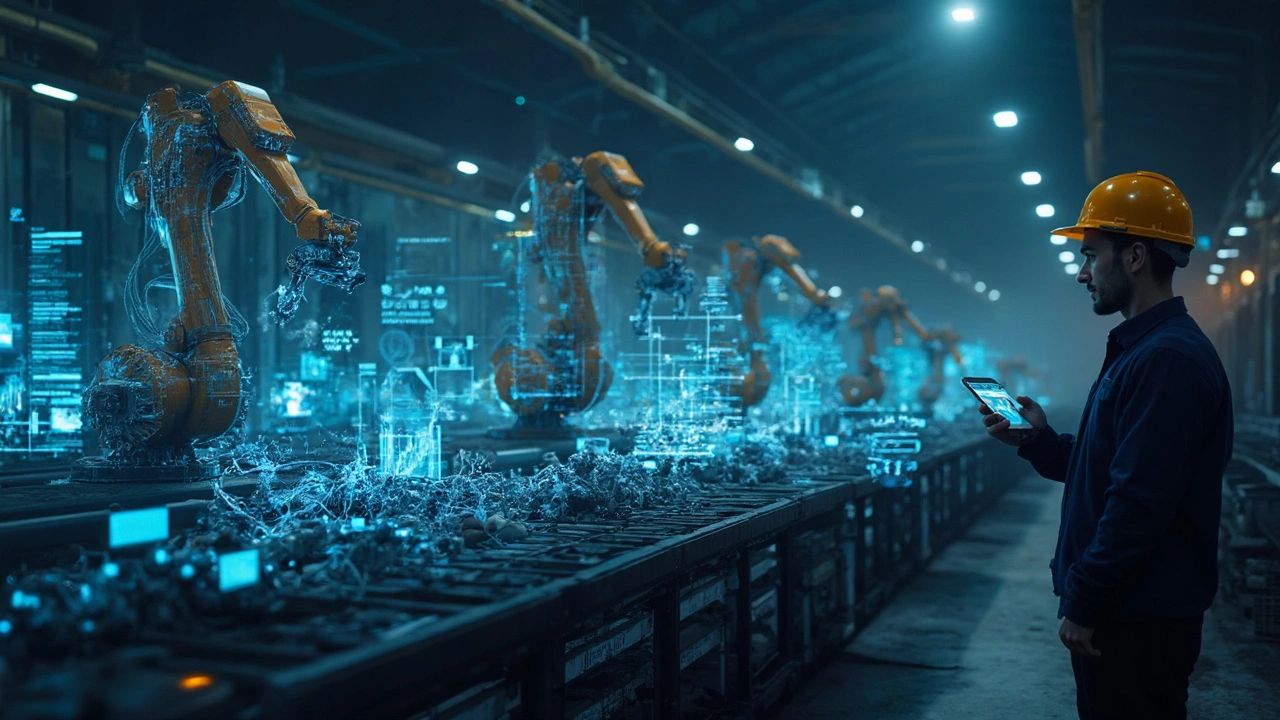
Интеграция в сервисное обслуживание
Вот где 3D моделирование в машиностроении реально раскрывает свой потенциал — это сервисное обслуживание техники. Уже давно крупные заводы и сервисные центры эксплуатируют цифровые копии агрегатов, чтобы ускорять и упрощать ремонт. Персонал может посмотреть, как деталь установлена, какие ещё элементы рядом, сразу увидеть, что и где менять — всё это экономит время и снижает риск ошибок.
Многие производители оборудования, например, Siemens или Caterpillar, создают для клиентов целые библиотеки цифровых инструкций на основе 3D моделей. Механики просто заходят на планшете или ноутбуке в нужную сборку и получают интерактивную подсказку — какой инструмент брать, где откручивать, как правильно поставить новую деталь. Для начинающих специалистов это просто спасение.
Ещё одна фишка — быстрая идентификация нужной запчасти. На модели видно маркировку, размеры, даже артикул. Это избавляет от путаницы и ускоряет заказ комплектующих. В случае сложного ремонта — достаточно просто нажать на нужную область модели, чтобы получить список совместимых деталей и инструкций по установке.
- Снижение времени ремонта минимум на 20% — такие данные приводили на одном из московских заводов после внедрения цифровых инструкций.
- Менее опытные сотрудники совершают ошибок меньше на 30% благодаря 3D-подсказкам.
Если добавить сюда возможность работы с цифровыми двойниками через VR или AR — это вообще новый уровень. Специалист видит инструкцию прямо на реальном объекте, не отвлекаясь на бумажки или видеоуроки. А если твоя техника работает на другом краю страны — сервис-инженеру достаточно иметь доступ к облачной базе 3D моделей и всё будет под контролем.